An example of a concentrating solar plant that uses dry cooling is the Ivanpah Solar Plant,
which is in the California Mohave Desert 40 miles southwest of Las Vegas, NV
–Kevin Grant/Shutterstock Photo
Clean and Dry: Water-Free Cooling for Solar Energy
NEXUS scientists investigate more efficient dry cooling systems for thermal power plants
By Jane Palmer
October, 2016
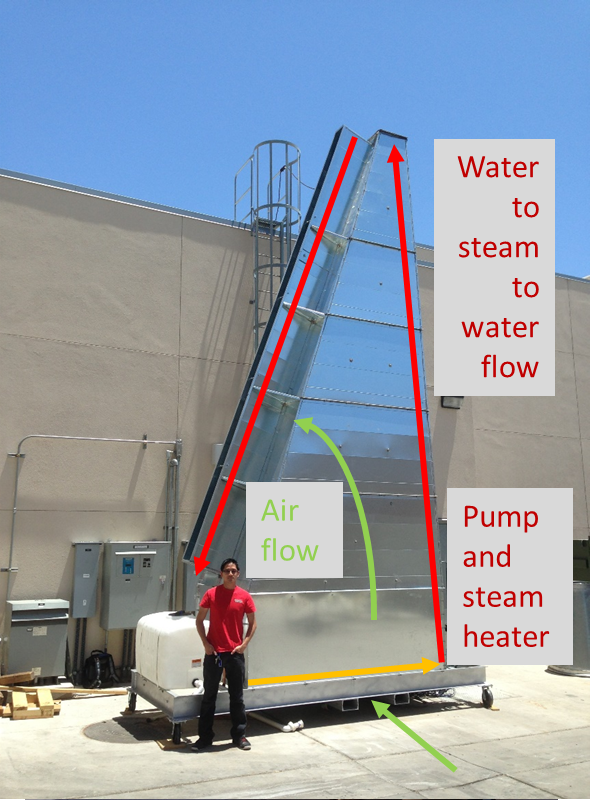
Former UNLV student Raymond Planas (graduated) at the Dry Cooling System Showing Two Flows
–R. Boehm Photo
Testing an Optimal Heat Handover
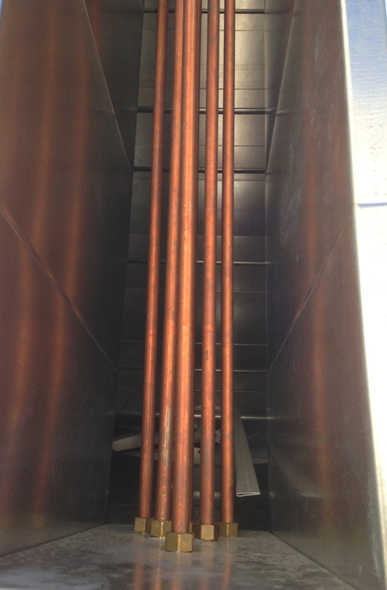
20 ft long slanted cooling tubes
–R. Boehm Photo
Looking to the Models
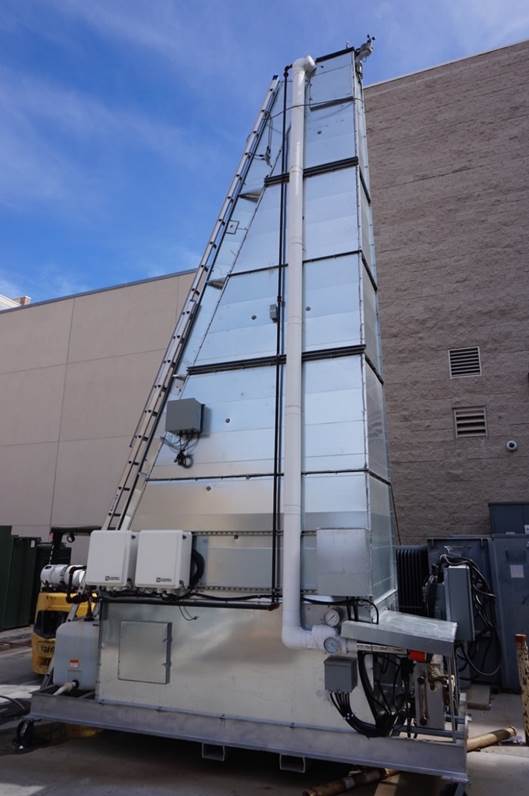
Fully Completed Dry Cooling System
–R. Boehm Photo
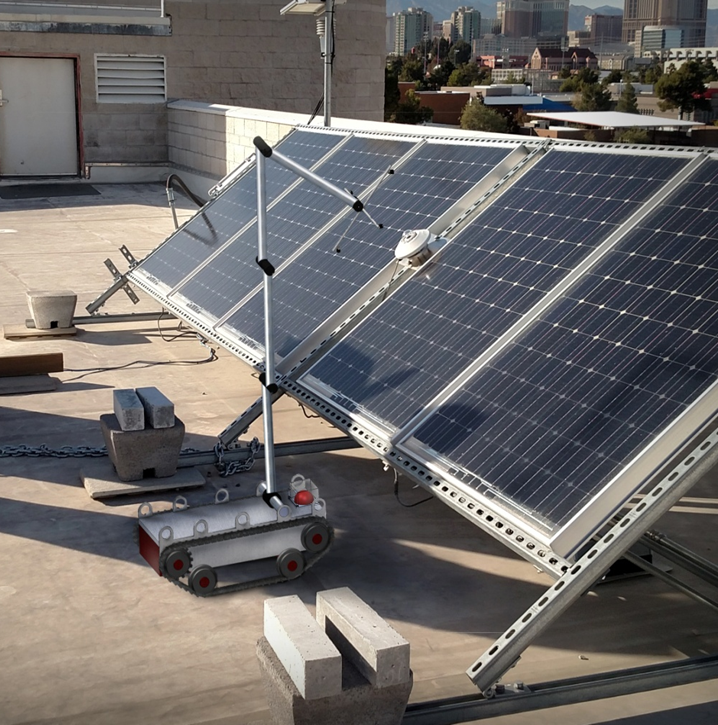
Helios Paneling Cleaning Robot
–E. Yfantis Photo
_______________________________________
Minimizing the Water Use of Solar Energy
_______________________________________
NEXUS researchers are exploring other ways to reduce solar energy production’s water footprint, in addition to developing more efficient dry cooling systems. The project’s scientists are also seeking to understand the nature of dust accumulation on photovoltaic panels and developing techniques to prevent these coatings, thereby cutting the volume of water needed for cleaning. NEXUS researchers are also investigating whether non-drinking, lesser quality water can be used to wash solar panels and using robots to clean panels in a way that optimizes water use. “Our NEXUS research will result in both less water use and land area needed for solar development, which will reduce environmental impact and lead to better economics for the system,” says Dr. Gayle Dana, Nevada’s Project Director for the National Science Foundation EPSCoR Program.
_______________________________________
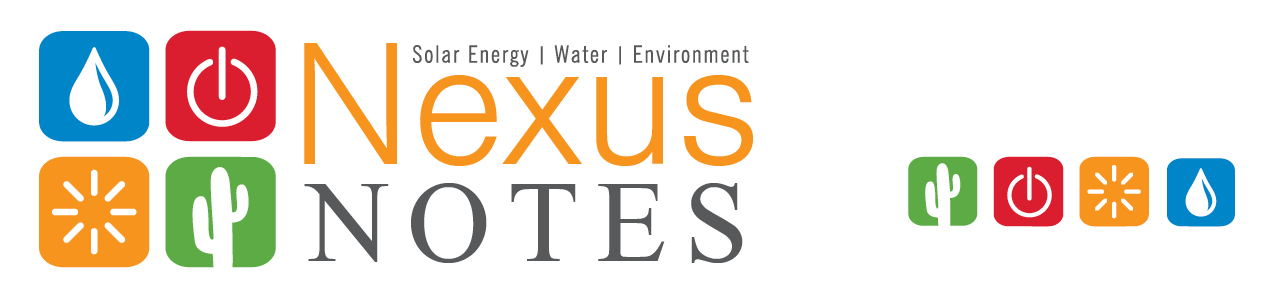
_______________________________________
NEXUS Notes is a monthly publication of the Solar Nexus Project, which is a five-year research project funded by the National Science Foundation’s Experimental Program to Stimulate Competitive Research “EPSCoR” (grant #IIA-1301726) focusing on the nexus of (or linkage between) solar energy generation and Nevada’s limited water resources and fragile environment.
Any opinions, findings, and conclusions or recommendations expressed in this material are those of the author(s) and do not necessarily reflect the views of the National Science Foundation.
_______________________________________